SDS management of hazardous substances: it is often experienced as time-consuming, complex and labor-intensive. Nevertheless, it is important to have an up-to-date Register of Hazardous Substances in your company, with correct and reliable information regarding the substances. The Safety Data Sheets (SDS) are an important source of information for this. But despite the fact that your suppliers are legally obliged to provide the correct and complete SDSs, in practice it is not always easy to complete your register and keep it up-to-date. In this blog we present 5 tips to get and keep your SDS household in order, without using expensive and perhaps superfluous SDS management solutions.
1. Central reception of SDSs
A simple but in our view effective start of an up-to-date Register of Hazardous Substances is a central email address to which your suppliers can send the SDSs. It is also advisable to make an agreement with your Purchasing department that a chemical product cannot be purchased (or the invoice is not paid until) after receipt of the corresponding and most recent SDS.
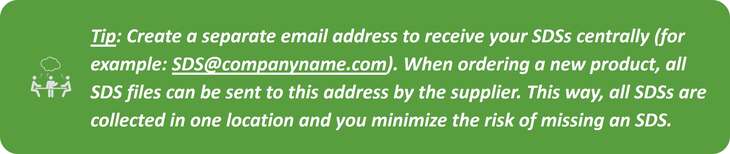
2. Quality of an SDS
It is important that an SDS is of good quality and complies with the CLP (Classification, Labeling and Packaging) regulation. According to this regulation, an SDS must meet a number of criteria in order to be considered of sufficient quality. To check whether an SDS complies with the applicable CLP regulations, you can ask yourself the following questions:
- Was the SDS created or updated after December 1, 2010? - From this date, new rules apply to the SDS format.
- Is the format of the SDS correct? - The SDS must consist of 16 sections/chapters.
- Is the SDS type (extended-SDS, SDS-TIUSSC, SDS) clear? - There are different types of SDSs depending on the quantity produced and the hazardous properties of the substance.
- Is the product/substance sufficiently identified (e.g. H-phrases, composition)? - An SDS with only R(isk)-phrases instead of H(azard)-phrases does not comply with the regulations, even if the issue date is after 1 December 2010.
- Is the supplier included in the SDS? - It is mandatory that the correct supplier is listed on the SDS. If unsafe situations arise with the substance or product, it is important that you can contact the right supplier.
- Is the SDS in the right language? - In the Netherlands it is mandatory to have a Dutch SDS available.
If you still have doubts about the completeness or quality of an SDS, you can perform a simple check with the SDS-check. This tool has been developed by the government, is freely accessible and offers an automated option to contact your supplier.

3. Timely renewal of SDSs
It is desirable that companies use so-called expiration dates for incoming SDSs. This means that companies allocate a maximum time span of, for example, 1 year to SDSs to ensure that the most recent version is present in the system. In practice, we see that products that are not often ordered and/or delivered are not provided with the correct SDS. By asking the supplier for the corresponding SDS at the time of product delivery, you are assured of the most relevant SDS that belongs to your product stock.

4. Extra attention for extended SDSs in accordance with REACH
Since the introduction of the REACH legislation, extended SDSs have been sent by suppliers. In addition to the usual 16 chapters, an extended SDS has an appendix with exposure scenarios. An exposure scenario is the set of conditions (both operational conditions and risk management measures) describing how the substance is manufactured, and how the manufacturer controls or recommends downstream users to control human and environmental exposure. From the moment you receive an extended SDS, you have 12 months to demonstrate that you are working with the substance in accordance with your supplier's safe work instructions, this is also referred to as the 'use-compliance check'.

5. Outsource SDS management or do it yourself?
There are several providers that relieve companies of the burden of managing SDSs. In addition to the fact that these services can be relatively expensive, it may well be that not all the necessary information is provided. This includes the lack of an exact date of receipt of an extended SDS and the risk that an SDS from another supplier will be delivered. The fact is that you should only have SDSs from your own suppliers, so that you can quickly contact the right supplier in risky situations. In addition, when companies apply a maximum time span, there may be a risk that an expired SDS is present in your registry.
Additionally, it is good to realize that with this type of service you often do not automatically have all the information in order to carry out the risk assessment (in accordance with the 4-step plan of the Dutch Labor Inspectorate) in order to comply with the Working Conditions Act. For example, when an SDS is received for a product, it often lacks the necessary information per substance in the product. Information such as limit value and vapor pressure per substance are essential to carry out an accurate risk assessment. In the case of outsourcing, this information must be defined and applied by yourself.

SDS management & Chemrade
With the tips above you can already take some important steps to get a grip on your incoming SDSs yourself. While Chemrade mainly focuses on the register and risk assessment of hazardous substances, there are also opportunities to use the platform for efficient and up-to-date SDS management. Each product and/or substance can be provided with the most recent (as well as previous) SDS. By automatically uploading the SDSs to the cloud, a single environment is created where you can collect and view all SDSs. When using expiration dates for SDSs, Chemrade offers the option to track expired SDSs with timestamps and version control in the SDS reporting functionality. End user can use this information to monitor and replace SDS versions if necessary.
Finally, Chemrade's Substance Database offers a solution if you want to assess mixtures of which individual substance properties are unknown. The fully managed Substance Database can provide up-to-date substance information required for risk assessment. Finally, Chemrade's reporting function offers an excellent opportunity to create an overview of your SDS household including receipt data, suppliers and contact details.
Would you like to know more about what Chemrade can do in SDS management and risk assessment of hazardous substances? Feel free to contact us for a demo!